Recoil lines - Rerolling lines - Rewind lines
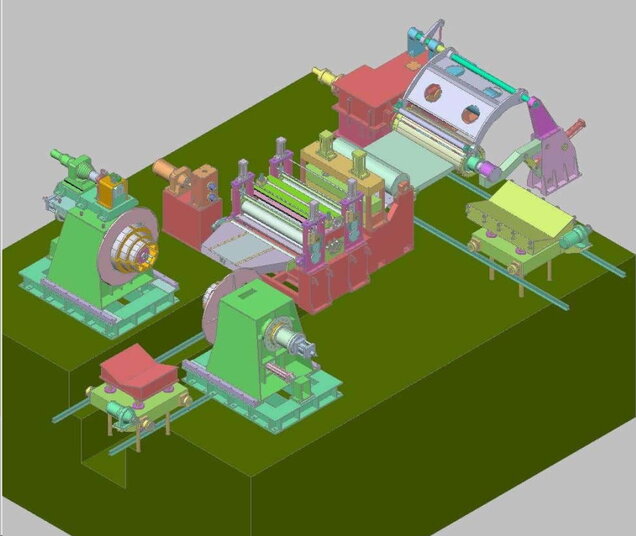
From Coil to Coil
Recoil-Rewind Lines
Recoiling and baby coil production
The line starts with big mother coil and it is used to produce smaller coils (approx 1-3 tons) which are used, in particular, in the construction industry
The production line is also able to produce small coils (so called baby coils) with a length of approx 30 - 150 m in zinc, copper, aluminium, pre-painted steel used mainly to manufacture parts for roofing in the civil engineering industry.
These baby coils are then stacked and packed in groups of 5/6 units, with a vertical axis, on Euro pallets.
We have developed fully automated plants for the production and packing of baby coils, that are able to produce at a high rate, performing taping/strapping automatically, packing and positioning on pallets, including weighing and labelling.
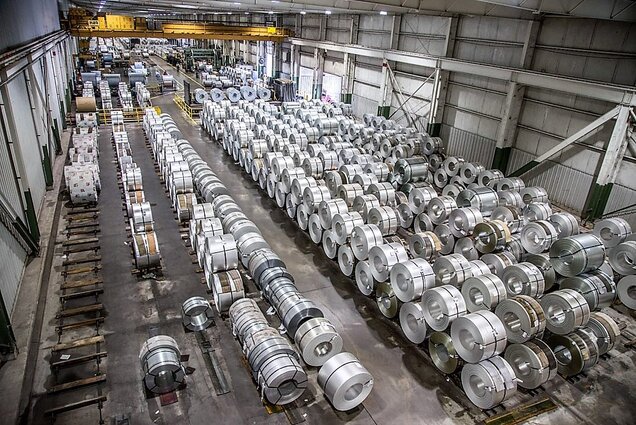
Precision Re-rolling of Strip Steel Products
Precision re-rolling of strip steel products is becoming important across a host of industries.
Coiling Lines
When working the coil surface, the strip must usually be wound with steady tension between Uncoiler and Recoiler: Companies who clean, brush, grind or coat coil materials are the users of the pressmach Coiling Lines.
The design of the Uncoilers and Recoilers that are utilized is specially adapted to cope with high forces and deliver absolute precision.
Dependent the application, the Coiling Lines are expanded with Straighteners and Coil End Joining stations (Welders) as well as Trim Shears.
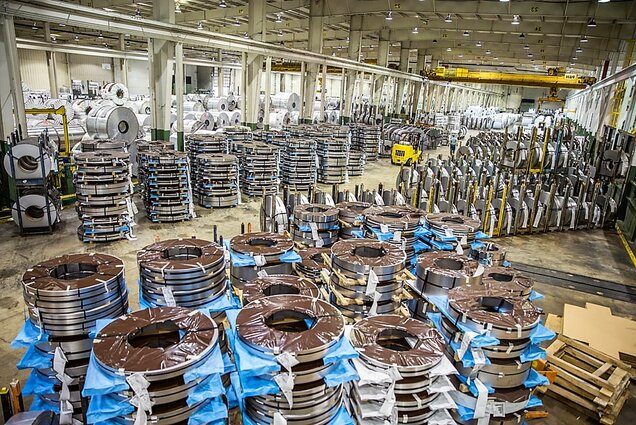
Coiling Line
Pressmach Coiling Lines have one core concern: to make sure, the strip is processed with precision and cleanness.
This is why we adapt the design of our Coiling Lines so we can use high tension and edge monitoring. Consequently, we run large drive forces – even for small cross-sections. The machine components are therefore built especially stiff and high-strength to absorb and convey all that power. To ensure an unobstructed processing or the commercial sale of the finished coil, it is necessary to rewind with highest layer-to-layer precision which we gain by the use of Coiling Line- special edge monitoring controls together with high precision traversing rails for motorized lateral adjustment of the Rewinder. That same precision is realized in the support of our customer – whether technical or coordinating.
Performance data:
- up to 40 t coil weight and approx. 18 mm material thickness
- max cross-section approx. 2200 x 8 mm
- max winding speed approx. 100 m/min
Common Applications:
- Feeding of coil stock into stamping or blanking presses with successive recoiling of processed material
- Feeding of coil stock into different coating or surface-treating machines with successive recoiling of processed material
- Coil-exchange from large master coil into several smaller coils, e.g. within steel service centers
Typical Compilation:
- Pull-off or pay-off reel with loop control
- Powered straightener to remove coil-set and flatten coil material
- Roll-feed with servo control or set of pinch rollers to feed material
- Strip-brake in front of recoiler to ensure tight recoiling
- Powered Recoiler with loop control, to pick up processed coil material from loop in front of strip brake
- Peripheral guarding with electric interlock
Additions & Extensions:
- Shear to cut off coil material for desired coil sizes
- Coil cars for pull-off / pay-off reel and recoiler
- Various hydraulic and motorized features and components to enhance capacities and level of automation