Forging Heat Sink Manufacturing Press - Cold Forming Extrusion Press for heat sink production
With PURE ALUMINIUM cold-forging technology heatsink, the heat dissipation is 3 times better than die-cast aluminium.
Heat sink production by cold forging
Heat sink production by cold forging extrusion
Cold forging of Heat Sinks and Pin Fin Heat Sinks is a highly precise manufacturing process in which the workpiece is formed under high pressure and low temperature. The process ensures that no air bubbles, porosity or other impurities are trapped in the material, and thus produces products with exceptionally high quality.
Four column cold forging hydraulic extrusion press
Pillar type cold forging hydraulic extrusion press
Four column cold forging hydraulic extrusion press - Pillar type cold forging hydraulic extrusion press
50 - 800 Tons Servo Hydraulic Pressing Power with pillar guiding
Use servo control system to save energy 50-70%.
2. Pressure stability,pressure error ±1bar,repeatable positioning accuracy up to±0.02mm.
3. Low failure rate,automatic alarm and fault indication,one-button reset function.
4. Remote maintenance service can be realized.
5. Can set up multi-stage pressure, multi-speed and contiouns fixed-pressure function.
6. Adopting an integral frame structure, high strength, low distortion and durability.
Sliding cold forging hydraulic extrusion press
Frame Precision Hydraulic Molding Machine - H-frame cold forging hydraulic extrusion press
Sliding cold forging hydraulic extrusion press - H-frame cold forging hydraulic extrusion press
100 - 1500 Tons Servo Hydraulic Pressing Power with Frame guiding
Frame Precision Hydraulic Molding Machine
1. Using advanced hydraulic system, more steady, safer and more reliable.
2. Pressure, stroke and pressure keeping can be adjusted according to processing requirement.
3. Four columns are made of high-strength alloy steel with hard chrome plated surface and good abrasion resistance.
4. The moving bolster and worktable are equipped with optional ejecting cylinder, which meets different ejecting requirements of different products.
5. Digital control is achieved with PLC programming circuit design and touch panel operating system.
COLD FORGING For Heat Sink Production
Copper & Aluminum Heat Sinks
Cold forging is a manufacturing process in which the aluminum or copper heat sink is formed by using localized compressed forces. Fin arrays are formed by forcing raw material into a molding die by a punch. The process ensures that no air bubbles, porosity or any other impurities are trapped within the material and thus produces exceptionally high quality products
Aluminum A1060
Aluminum AL1100
Aluminum A6061
Pure Copper CDA 110
</= 120mm max diameter/width
</= 80mm max height
25:1 fin height to minimum gap ratio
>/= 0.7 mm fin thickness
High performance electronics
Multi-chip modules
LED cooling
Elliptical or round fins
Improved mechanical strength
Better control of tolerance
Improved surface finish
High production rate
Heat Sinks
Which heat sink to chose??
Extruded Heat Sinks
Extruded heat sinks are the most common heat sinks used for thermal management. Extruded heat sinks are generally used in medium power systems both in natural and forced convection. The extrusion process, pushing hot raw aluminium through a steel extrusion die to create the desired profile allows for innumerable complex shapes to be manufactured. Many standard shapes are available but modifying the profile shape changes the surface in contact with the air and consequently the heat dissipation capability. Columbia-Staver can supply standard profiles or engineer a heat sink shape to achieve optimal performance in the space available. After cooling and ageing, the material is cut to the final heat sink length and any additional features such as holes or pockets can be added.
Extruded heat sinks can be supplied raw or with a finish, such as anodizing, electrophoresis or powder coating. Certain finishes can alter the emissivity, which can enhance thermal performance.
Cold Forging
Cold forging is a cold working process. Aluminium is squeezed by a press into the closed die, the resultant heat sink taking on the shape of the void in the die. This process is also known as cold heading. Cold forged heat sinks often have high performance compared with other technologies, mainly because any increase to the surface area of a heat sink will almost always result in improved thermal performance. Forged fins can be made almost perfectly straight, allowing for more fins per square inch than in an extruded product. The part is formed under high pressure which controls the grain structure and results in improved thermal performance The fins can also be formed into an elliptical or circular shape enabling airflow from any direction – a big advantage in some applications.
Stacked, Zipper, Folded Fin Heat Sinks
Stacked or zipper fin heat sinks can be an alternative to both extrusion and skived when looking for high density structure. Unlike the one piece skived fin heat sink, a zipper fin heat sink is an assembly of a base and a separate fin stack. The fin stack is created using a set of individually stamped fins, these fins are stacked or “zipped” together to form a block of fins. The finished fin stack is then soldered or bonded to the heat sink base. Zipper fins are most often used with a base plate but they can also be used with heat pipes. A hole or holes are stamped into the fins and the fin stack set is placed on a series of heat pipes to form the heat sink. Zipper fins can be manufactured from either copper or aluminium. Zipper fin heat sinks can also be customized with heat pipes embedded into the base plate to enhance performance.
Skived Heat Sinks
Skived fin heat sinks can be used as an alternative to extruded heat sinks when looking for a fin density which can’t be achieved by extrusion technology. Skived heat sinks can be manufactured from either copper or aluminium and usually have 0.5mm thick fins, although fins as thin as 0.2mm are achievable. In this manufacturing technology the heat sink fins are literally carved out of the base of the Heat sink. In the machine, specially designed blades slice the surface cutting very fine and thin fins into the raw metal block at a shallow angle, the fins are then folded vertically and aligned with the previous fin. As the fins and the heat sink base are part of the same block of material, skived fin heat sinks give excellent thermal conductivity between fin and base. Skived heat sinks can also be customized with embedded heat pipes to enhance performance if required.
Die-Cast Heat Sinks
Die casting is the process of injecting liquid metal under high pressure into a high precision mould created using two hardened tool steel dies. One of the big advantages of die casting is that it is an effective method of forming complex shapes of high tolerance with little need for post moulding machining. Mounting holes, slots, pins etc can be added with little cost penalty.
Heat sinks can be die-cast in both aluminium and zinc materials, however the thermal conductivity of the Die Cast material is not as good as that used in extruded heat sinks and die casting tooling is generally more expensive than extrusion tooling. A variety of surface treatment options are available depending on the casting material these include anodising, electrophoresis and powder coating.
Production cost of Cold forging process for Heat Sink production
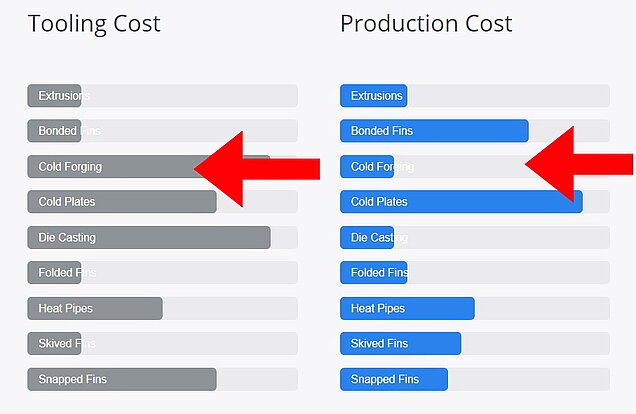
Benefits of a Forged Heat Sink
Aluminium extruded and die cast heat sinks dominate the industry. As devises that require cooling becoming smaller and heat generation increases, companies are forced to look for a more efficient cooling solutions. One of them is FORGED heat sinks.
Comparing extruded heat sink design to bonded fins type assembly, extrusions will outperform by large margin due to bonded assembly. Thermal transfer is somewhat reduced by the bonding agent added thermal resistance. There are five common techniques that are used to manufacture heat sinks out of one piece:
- Die Casting
- Machining
- Extrusion
- Forging
- Skiving Fins
Let’s discuss performance of each of those types of heat sinks:
Thermal Conductivity
Diecasting is a method for manufacturing complex shapes in high volumes and low cost. Initial tooling cost outlay is high, but the parts cost during the production run is relatively low. Drawback is porous structure as the molten aluminium alloy cools in the die-set it expands creating voids. The porous structure weakens the part and adds to thermal resistance to the heat sink.
Extruded aluminium alloy heat sinks are most cost effective way for manufacturing linear shapes. The drawback is the limitation in the freedom in design, but this method requires low cost tooling. During the extrusion, alloy is heated below melting point and force-feed thru the forming die-set. However the grain structure cannot be controlled evenly and shape of the heatsink cannot be optimized completely thus somewhat reduce thermal performance.
Machined heat sinks: This way of producing is due to high CNC machining costs of machined heat sinks, economically feasible only for prototyping and special low volume and high cost products. Cost of production is limiting this heat sinks to prototype production.
Forging is the most effective method to produce complex shapes in high quantity and also offers interesting thermal advantages due to processing alloys at room temperature. Due to the nature of the forging process, part is formed at high pressure and low temperature, process that allow better control of the grain structure. Making heat sinks stronger and better conductors of heat.
Skiving fins is the latest technology, which is very promissing and grows exponential due to the many benefits: heat sink is formed out of one block with the highest cooling capacity per weight of material. See here for more info on this subject.
The cold forging process produces heat sink with 13% better thermal conductivity over extruded and 60% over die-cast part. Note that in this test average samples been tested. Best examples of each heat sink likely to produce better results somewhat dampening large outperformance by forged part.
Heatsink Surface Area
Increased surface area of the heat sink will yield lower thermal resistance and better component cooling, but only if boundary layer is not formed and fins close proximity do not prohibit flow of air. When designing extruded part, fins must be tapered so that the aluminium alloy will pass through the tool without breaking it. The number of fins in an extrusion limited by strength of the die set and the size of the extrusion. These restrictions have negative impact on the surface area.
Forged fins require lesser taper for extraction from the tool, allowing for more fins per given heat sink size. Heat sink fins can also be formed in to elliptical shape if required. The forged heat sink increases the surface area by 15% without increasing the size. The result is improved thermal performance.
Reduced Cost
Depending on design, forged heat sink process can simplify manufacturing process. In cases when secondary operation required when working with extruded or die-cast heat sinks in forging process this can be part of a single operation. That can greatly influence cost of the finished product.
The forging process has fewer limitations to forming heatsink shapes and fin designs. A forged part is formed in two dimensions within the stamping tool creating complex shapes without the need for secondary operations. Holes, chamfers, pins, elliptical fins and steps are created in the one tool in a single operation. The forged heat sinks allow designers to creates unique shapes and fin designs that can be achieved in the forge tool in a single operation.
In plus, a (copper) spreader plate can be inserted in to the forging tool following by the aluminium alloy slab. When pressed in to the die, aluminium formed in to heat sink shape and creates tight fit over the copper base, with minimal added thermal resistance.
Conclusion
Forged heat sinks together with Skived fin heat sinks offer many advantages over machined, die cast and extruded processes. The improved thermal performance due to aluminium grain structure coupled with the increased surface area without increasing the size of the heat sink and low process cost are main advantages.
Cold forging can also produce heat sinks of the complex shapes such as elliptical fins, staggered fins, round pin arrays, steps, all within the tool. Finally, precision forged heat sinks can often be manufactured at a lower cost because most operations can be performed in the tool and secondary operations are reduced.
Forging is also the most effective method for forming copper. Copper is difficult to extrude because it must be heated to high temperatures to soften the metal, making it challenging. Forging is a cold process, and copper heat sinks can be formed with minimal waste.
What Are the Benefits of Cold Forming of heat sink elements?
Cold forming/forging is an eco-friendly manufacturing process in which the workpiece is formed under high pressure and low temperature. The process ensures that no air bubbles, porosity or any other impurities are trapped within the material, and thus produces exceptionally high quality products.
Compared with other manufacturing methods (machining, die casting, extrusion, hot forging, etc.), cold forging offers the following benefits:
- Improved mechanical strength
- Improved surface finish
- Better control of tolerance
- Efficient use of raw materials
- Reduced energy consumption
- High production rate
- Low overall cost
In making aluminum heat sinks, cold forging can produce pins that are 50 times as tall as their diameters – an aspect ratio that is considered impossible with other methods, such as die-casting or extrusion.
Unlike stamped-fin or bonded-fin heat sinks, the pins on a forged heat sink are an integral part of the base – they are simply squeezed out of the base. There is no air gap or thermal interface between the pins and the base. Heat can dissipates easily from the base to the pins without additional resistance.
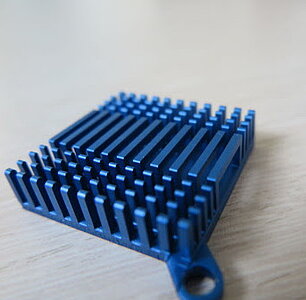
A Cold forged heatsink is a good alternative to casting to form complex shapes with excellent thermal conductivity. The Cold forging process can make almost perfectly straight allowing for more fins per square mm. Cold forged heatsink shapes include plate fin heat sinks, round pin heat sinks, and elliptical fin heat sinks. Cold forged heatsink manufacture lends itself very well to using copper because high temperatures are not required to shape the copper heatsink, and it can be formed with minimal damage. Secondary machining operations such as hole, chamfer, and steps can be usually included in the cold forged heatsink manufacture reducing waste. Forging involves the shaping of metal using localized compressive forces.
A Forged heatsink is manufactured using a modification of this process called cold forging. Cold forging uses high pressure and low temperature to ensure that no air bubbles, or other impurities are trapped in the material. This improves the thermal properties of the heatsink, and increases the density of the material. Pressmach utilizes and delivers on demand special open die tooling and intense high pressure presses to produces high precision heatsinks with high aspect ratios. A Forged heatsink is typically manufactured one part at a time, and can be can be made from AL 6063 or C1100. Aspect ratio up to 35:1 are feasible, and no draft angles required on fins. Fins can be round, elliptical, straight or any combination on the same part.
An added benefit of this process is that a forged heatsink of the same design can be manufactured with different heights using only one set of forging die. When working with high aspect ratio, or dense fins a forged heatsink has no thermal interface between the fins/pins, and the base which will provide better performance compared with stamped-fin or bonded-fin heat sinks. Heat distribution can be further improved in aluminum heatsinks by embedding a copper inserts into the base during the forging. As this process is fairly expensive, for small volumes it may be worth exploring extrusion with a cross cut to produce square pins. For larger volumes die cast is a good alternative.
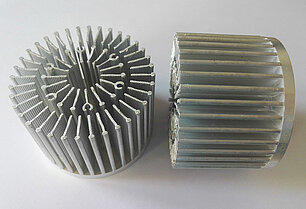
Cold forged heat sinks : simply superior thermal behavior
High performance heat sinks
Forged heat sinks offer advantages over machined, die cast and extruded processes. The improved thermal performance due to aluminium grain structure coupled with the increased surface area without increasing the size of the heat sink and low process cost are main advantages.
Cold forging can also produce heat sinks of the complex shapes such as elliptical fins, staggered fins, round pin arrays, steps, all within the tool. Finally, precision forged heat sinks can often be manufactured at a lower cost because most operations can be performed in the tool and secondary operations are reduced.
Forging is also the most effective method for forming copper. Copper is difficult to extrude because it must be heated to high temperatures to soften the metal, making it challenging. Forging is a cold process, and copper heat sinks can be formed with minimal waste.
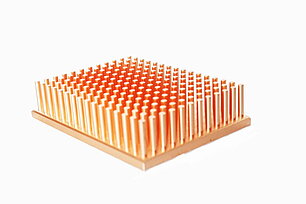
Copper pin fin cold forging heatsinks
Cold forged copper heatsink manufacturing
Cold forging is a highly precise manufacturing process in which the workpiece is formed under high pressure and low temperature. The process ensures that no air bubbles, porosity or other impurities are trapped in the material, and thus produces products with exceptionally high quality. The Cold forging process can make almost perfectly straight allowing for more fins per square mm. cold forging heatsinks shapes include plate fin heat sinks, round pin heat sinks, and elliptical fin heat sinks.
Cold forged heatsink manufacture lends itself very well to using copper because high temperatures are not required to shape the copper heatsink, and it can be formed with minimal damage. Secondary machining operations such as hole, chamfer, and steps can be usually included in the cold forged heatsink manufacture reducing waste. Forging involves the shaping of metal using localized compressive forces.
More Information on Skiving heat sinks
Heatsink Fin Skiving Machines
Skiving thin Fins for super efficient heat dissipation on heat sinks
Skived Fin heat sinks are the best alternative to extruded heat sinks when looking for a fin density which can’t be achieved by extrusion technology. Skived heat sinks can be manufactured from either copper or aluminum. Today, skived heatsinks are breaking through the limitation of the thickness and length ratio of conventional heat sinks and our machines can produce high density and very high efficient heat sinks. Super high and extreme thin fins and extra-long heat sink structure can be produced by our dedicated skiving machines using high skiving precision cutting technology. Fin Skiving machines use a single block of material such as copper or aluminum and cut out fins with high density. The fins and the base is “one piece”. So skived fin heat sink efficiency is till two times higher than traditional heat sink. Thermal conductivity efficiency can reach 100% of the profile material. Skived heat sink widely used in photovoltaic industry, electric vehicles, inverters, communication products, led light in green house and so on.