Single End Reels
Single End Reels are built to handle up to 30TONS coils with stock widths between 200mm and 3000mm. Reels can be motorized or pull-off, depending on the application, and can use a variety of loop control methods. Double end reels or load cars can be used to improve coil change over time and increase efficiency. Pressmach Reels are engineered and manufactured by the highest standards to fit your specific press room needs.
Single end decoiler machine
Single Reel
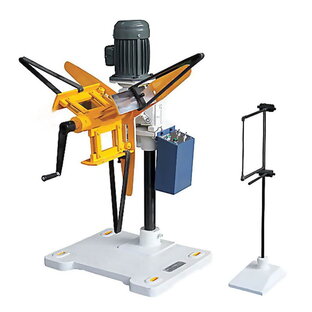
With powerful motor driven, the decoiler machine can handle more complex and high requirements roll conditions.
Manual decoiler machine is a good choice if your production is only a limited types of products and be sure your products is the small hardware parts and no high strength material.

Double End Reels - uncoiler
Double End Reels are built to handle up to 15 ton coils with stock widths between 200mm and 2000mm. Reels can be motorized or pull-off, depending on the application, and can use a variety of loop control methods. Power rotation and load cars can be provided to improve coil change over time and increase efficiency. Pressmach Reels are engineered and manufactured by the highest standards to fit your specific press room needs.
Double Head Uncoiler
Double ends decoiler machine
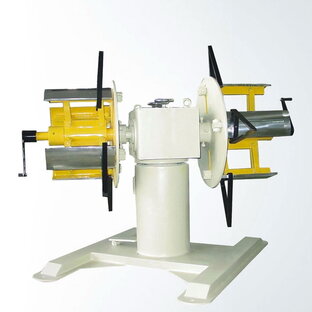
Manual decoiler machine is a good choice if your production is only a limited types of products and be sure your products is the small hardware parts and no high strength material.
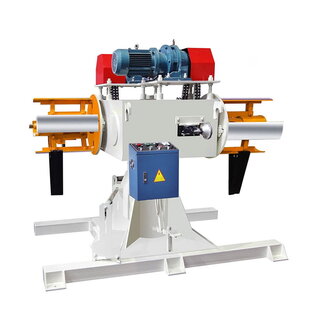
With powerful motor driven, the decoiler machine can handle more complex and high requirements roll conditions.
Multi-stations Coil Decoiler
Advantages of Motorised Steel Roll Decoiler Machine
Uncoiler or Decoiler machine is an essential part of modern press stamping lines. Basically there are 2 types decoiler for stampers’ choice, the manual one or the motorized one. Manual decoiler machine is mainly used for small metal rolls work, like connecting terminal production with thin cold rolled steel strip, or the close button production line with narrow metal tape.
1. Advantage: good to work with all kinds of steel rolls
You production line may change time by time for different products and different orders. And different products need different size steel rolls. For metal rolls that weight is less than 500kg, and width is no more than 400mm, the manual decoiler may be able to work well. However, if any of the conditions we mentioned here is failed, the manual one will also fail to work. But for motorized one, you can hold back your worries. With powerful motor driven, the decoiler will easy to fit your special coil rolls’ conditions.
2. Advantage: able to handle high strengthen material
Each metal steels or alloy has its own physical strength, we can group them in two types, the common ones and strengthen ones. For common ones, it’s normally the HR/ hot rolled steel and CR/ cold rolled steel. For strength ones it’s normally the stainless steel and some high-alloy steel.
The high strength material is hard to manage, the high force between every rolls require extra power to ensure the decoiling procedure is steady. Motor power will provide the needed force to keep rolls de-coling in order.
3. Advantage: always prevent material to be scratched
If your customers’ order has requirements on its final product, and you are suffering quality surface problems that result in your high defective production rate, then you need to pay attention to choose the right decoiler machine.
How can the de-coiling machine effect the final products surface?
The de-coiling procedure is to unwind the steel rolls layer by layer. There are small space between layer and layer. And the extra space result in two close layers rubbing time by time during the un-coiling. Motorised decoiler rolling with its own power, so the uncoiling is managed. And managed uncoiling effectively prevent layers friction that damages the surface of your products.
Press Arm and Support Arm on Heavy Decoiler Machine
The press arm is used for heavy decoiler to press the outer ring of the material when it’s uncoiling, to avoid the problem of loose coil material when it’s uncoiling, at the same time, the pressure in the process of continuous discharging ensures the normal operation of uncoiling process, the supporting arm is used for lifting the head of the material after the material belt is unrolled, which is used to cooperate with the straightener machine to achieve stable feeding and avoid scratches on the edge of the material belt, these two optional devices are recommended to be used when the material thickness exceeds 2.0mm. When selecting press arm and supporting arm at the same time for heavy decoiler, it is usually combined with thick plate straightener machine or thick plate feeder machine to become thick plate 2 in 1 straightener machine and thick plate 3 in 1 feeder machine, therefore, Dongguan Henli machinery will explain in detail the operation method of the two models after selecting the pressure arm and the support arm:
- The pressing arm of the heavy decoiler is raised to a higher position, and at the same time, the supporting arm is reduced to a lower position to avoid touching when winding up.
- Press the oil pressure expansion and reduction button on the independent handle to adjust the expansion and contraction drum to less than the inner diameter of the material coil.
- The material reel shall be assembled into the swelling drum of heavy material frame by using line hoist or forklift truck, and close to the inner baffle arm to expand the swelling drum of heavy material frame to fix the material.
- Operating the press arm down to make the press wheel tighten the outer ring of the coil.
- Start running heavy decoiler, place the material head in the suitable position and lift the supporting arm to hold the material coil.
- Unlashing coil material, the electronic control box control moves to manual “inch-in” to drive the winding material, so that the material head is close to the intake port of the straightener machine, and the material head is bent by the oil-pressure feeding device of the straightener machine, so that the material head can enter the roller smoothly.
- The material head is bent by using the dynamic matching material of the decoiler and the oil pressure into the feeding guide device of the straightener to make the material head enter the straightening drum.
- Press down the front belt wheel that is clamp the material, and then put down the supporting arm and the oil pressure into the feeding guide device.
- Operating straightener makes material pass through straightening roller, and then feed into feeder. At this point, the whole equipment is ready for debugging, and the automatic feeding operation can be started.