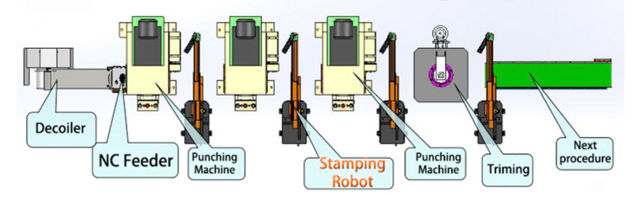
Robot Arm
Modern robots are mainly composed of two parts: the robot body and the control system. The robot body has the same action function as the human arm, can grasp objects in the space or perform other operations, and is composed of mechanical structure, driving device and transmission device; the robot control system is the motion command system of the robot.
The stamping mechanical robot arm belongs to industrial robot and is a special application of industrial robot in stamping production. In the robotic stamping automation line, as the main part of the automatic conveying system, the robot mainly completes the work of the sheet metal unstacking, the automatic loading and unloading of each press, the plate conveying and turning, etc. in order to replace the heavy and dangerous manual operation. The mechanical robot armmaintains the follow-up and interlocking of the press through the control system, and completes the robot's motion control, pneumatic and vacuum system monitoring and safety protection.
The specific selection of the robot is based on: the load capacity of the robot is determined by the weight of the work piece and the end picker; the working range of the robot is confirmed according to the distance between the presses; if the working range of the robot cannot meet the requirements for use, consider using the robot end extend arm or add the robot moving rail to expand the working range of the robot; finally, set the robot motion parameters according to technical performance requirements such as production speed.
Picker and Vacuum System
The end picker is the end effector of the robot for gripping the work piece. Since the work piece is a thin-walled sheet, it is suitable for grasping by the vacuum adsorption. The vacuum suction cup is arranged on the extension arm bracket made of high-strength alloy or carbon fiber material. The number of suction cups and their arrangement are determined by the specific work piece. And the suction cup is provided with a vacuum detecting sensor which detects the vacuum in the suction cup to determine whether the work piece is in place or not, and whether the work piece is dropped during the handling. The structure of the end picker is related to the shape of the work piece. Therefore, different work pieces and different stations need to be configured with different end pickers.
In order to prevent the work piece from falling during high-speed handling due to the failure of the vacuum system, it is considered to use two independent working vacuum generators to form a redundant vacuum system, and the suction cups of the two vacuum systems are staggered even if one system fails, the robot can still grasp the work piece and reduce the chance of accidents.
Centering Station
During the loading process, the loading robotic arm robot is required to accurately position the sheet into the press mold, so the work piece must be pre-positioned before the feeding.
According to its working principle, the centering station can be divided into gravity centering station and automatic centering station. Gravity on the centering station relies on the weight of the sheet itself to achieve positioning on the inclined workbench. This centering structure is simple, but different robot programs are required for different sizes of sheets; the automatic centering station adopts the stepping motor driving the stoppers distributed on the four sides of the centering station to realize the precise positioning of the work piece. Before production, manual teaching is carried out for different sizes of sheets, and the position of the stoppers is recorded by the encoder carried by the stepping motor. In the production process, different work pieces can be automatically positioned by selecting different programs. The structure and control are more complicated than the gravity center, but the loading robot only needs one set of programs.
Dual Material Detection Device
In order to prevent the mechanical robot arm from grasping the double material, a detection sensor is installed on the robot end picker for double material detection. The dual material detecting sensor is composed of a connecting portion, a sensor, a spring and a vacuum chuck portion. After the robot grabs the work piece, under the adjustment of the spring, the vacuum chuck is tightly attached to the sheet to ensure that the sensor is vertical and close to the sheet. The sensor adopts an ultrasonic sensor, and its working principle is that the thickness of the sheet is tested by ultrasonic detection, and by comparing with the thickness of the sheet preset to check whether the double material is detected, and the judgment result is input into the robot controller.